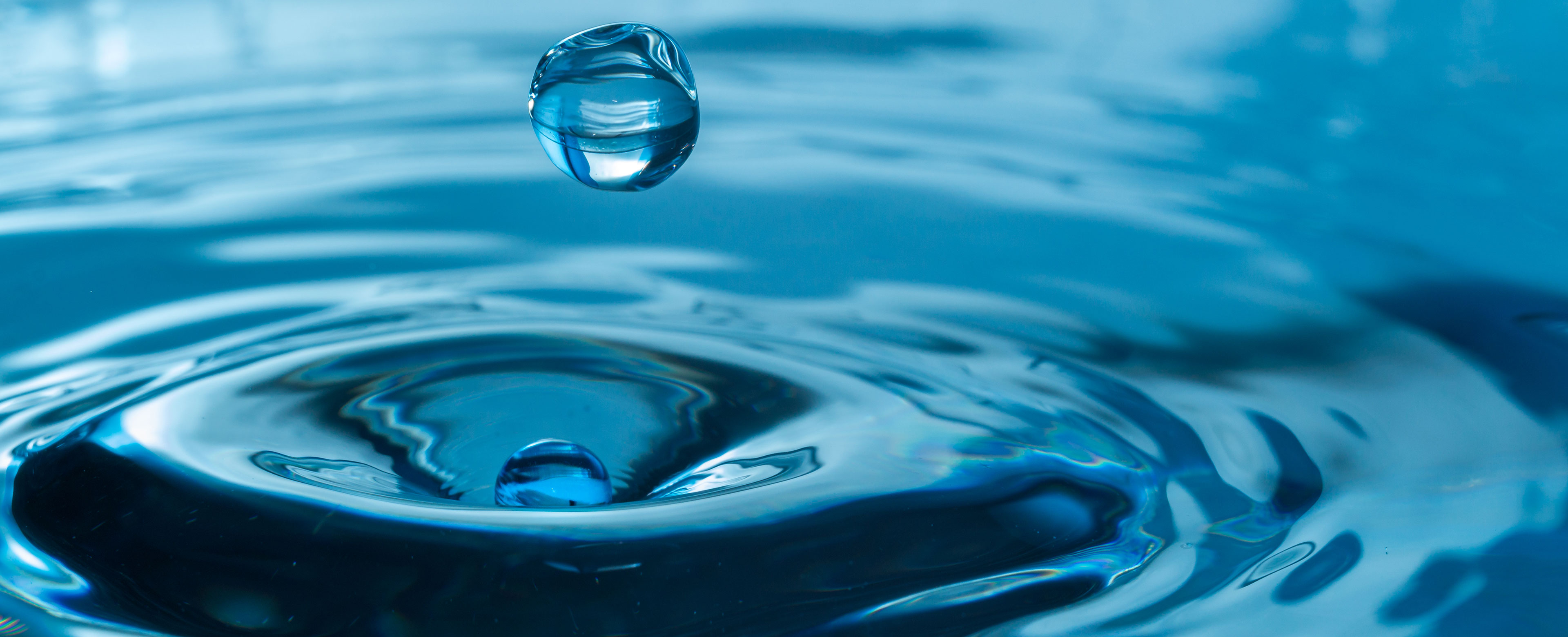
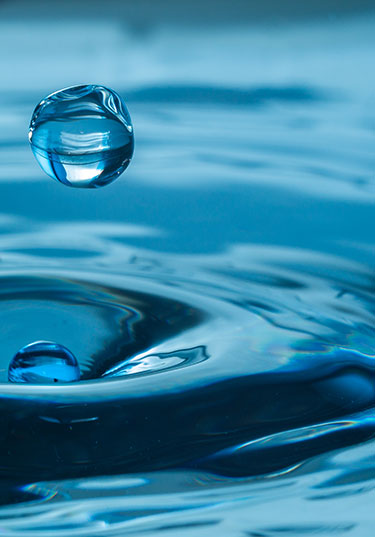
We have a dedicated team that takes the lead on EHS matters, called the Environment, Safety and Health (ESH) Team. Led by our Chief Safety Officer (CSO), this team oversees day-to-day EHS activity.
Our policy
Environment, health and safety management is one of our core business management principles. Our ESH Policy has been drawn up in response to a range of regulations and guidelines, and outlines the vision of our senior management team in this area.
As laid out in the policy, we strive to enhance the quality of our EHS provision through continuous technology development and commit to pursuing our sustainability agenda in partnership with the communities in which we operate. To read or download the full policy, please click here: ESH Policy
We provide training on environmental awareness for the workforce at our Gumi manufacturing facilities, including the executive team. In 2024, the topics covered by the training were: (i) understanding manufacturing management, (ii) promoting resource conservation and recycling, and (iii) waste management.
Environmental management system
Our environmental management system (EMS) is designed to ensure sustainable practices throughout our activities, thereby maintaining high corporate values through transparency and consistency. Underpinning our EMS is a process of “Plan, Do, Check, Correct”, as shown in the diagram below.
Diagram 1: Plan, Do, Check, Correct
EHS standards
Our EMS complies with a range of internationally recognized standards. These standards stipulate that ESH must be taken into account throughout all our business operations.
Specifically, we have adopted ISO 14001 and ISO 45001 (Environmental Safety and Health Management System), which have been operated by DQS Korea, an international certification agency, since 2004. We also maintain compliance with applicable local and international laws, including the Occupational Safety and Health Act of Korea, as well as customer requirements such as those relating to hazardous chemicals.
Our ISO certification scope applies to all business areas, including production, sales and product services, and is verified through annual internal audits. In addition, DQS Korea conducts external audits on an annual basis, as detailed in the ISO certification scope.
Environmental performance evaluation
Central to our EMS is our evaluation process, which follows the following steps:
1) Select – set indicators; rate importance and scoring criteria
2) Collect – collect data by indicator; transform data types; evaluate based on criteria
3) Review – evaluate results; modify indicators; set new standards
4) Improve – make improvement based on new standards
Through this process we have achieved a number of important environmental goals, including reducing our greenhouse gas (GHG) emissions, energy use, pollutant discharge, waste discharge and raw material use, as well as making improvements to our working environment.
The number of environmental objectives we have achieved through this method was 25 in 2023 and 22 in 2024.